20:43 on November 3rd, 2016, China's new generation carrier rocket Long March 5 which has the largest thrust blasted off in Wenchang Satellite Launch Center. Approx. 30 minutes later, the Load combination and rocket successfully separated and launched into the scheduled orbit, The maiden flight of rocker is a complete success. It is worth mentioning that an important part of the rocket has been developed by using SLM 3D Print technology!
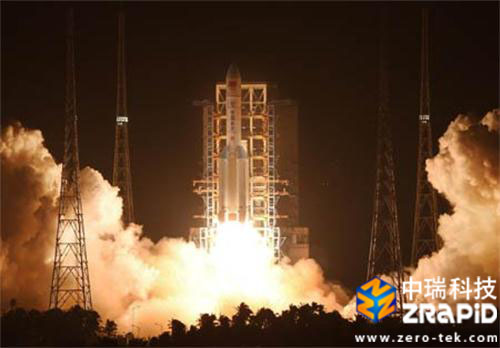
Long March 5 is the basic type of new generation non-toxic, non-polluting and green environment carrier rocket with a 5-meter diameter core, bundled with four 3.35 meter diameter boosters. It is approx. 57 meters long with approx. 870 tons takeoff weight. It has more than 1,000 tons of takeoff thrust, with near-Earth orbit 25 tons / Earth synchronous transfer orbit 14 tons carrying capacity. It is understood that advanced digital design has been firstly used in the development process of Long March 5 , starting the digital development of the rocket models. SLM 3D print technology has been also used in the development of its main force component - Titanium Alloy core-level bundled bearings. Although the force bearing component finally installed on the rocket is still manufactured using traditional way to ensure complete safety, it did have a 3D Print version for testing during the development process.
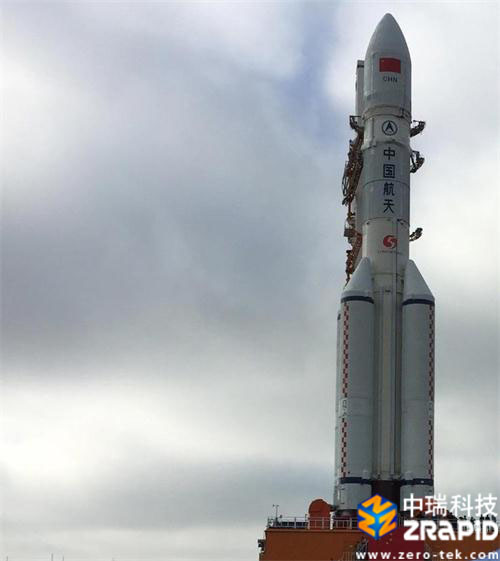
It is understood that this force bearing component was manufactured using laser synchronous powder delivery 3D Print technology by the China Aerospace Science and Technology Corporation plant 211. It is the first time using this technology to manufacture large-scale main force bearing key component, expanding the experience of 3D Print technology using in the rocket structure manufacturing applications / large-scale difficulty metal structure manufacturing.
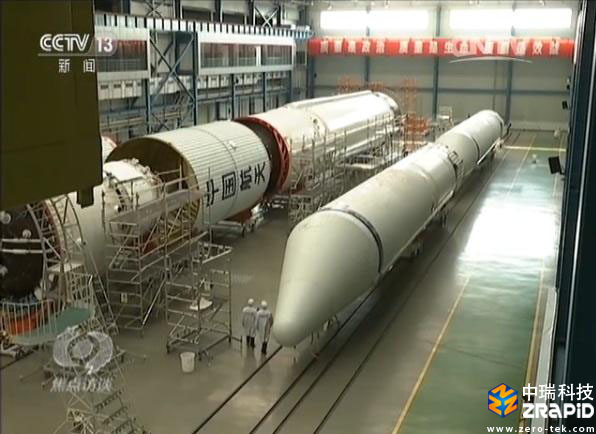
It is reported that the binding bearing is the main force bearing component of the carrier rocket, it requires high comprehensive mechanical performance. Current, it is mainly forged and then machined using high-strength steel. However, this process has some issues: cutting a large amount of material as well as requiring a long processing cycle.
In the face of the urgent need for new models to reduce the weight, the plant proposed to use a higher strength Titanium Alloy material and laser synchronous powder delivery 3D Print process to achieve the one-time forming of binding bearings. After comprehensive research, the testing product of this plant successfully passed the composition / organization performance / surface quality and internal quality and other types of evaluations, the performance achieves the level of forgings, and reduces 30% less weight than the original design.
original text : China Aerospace daily
ZRapid Tech - Innovator of 3D printing technologies. Click here to enter: http://www.zero-tek.com/